- Home
- How to Select the Right Cable Tray: Ladder vs. Perforated
How to Select the Right Cable Tray: Ladder vs. Perforated
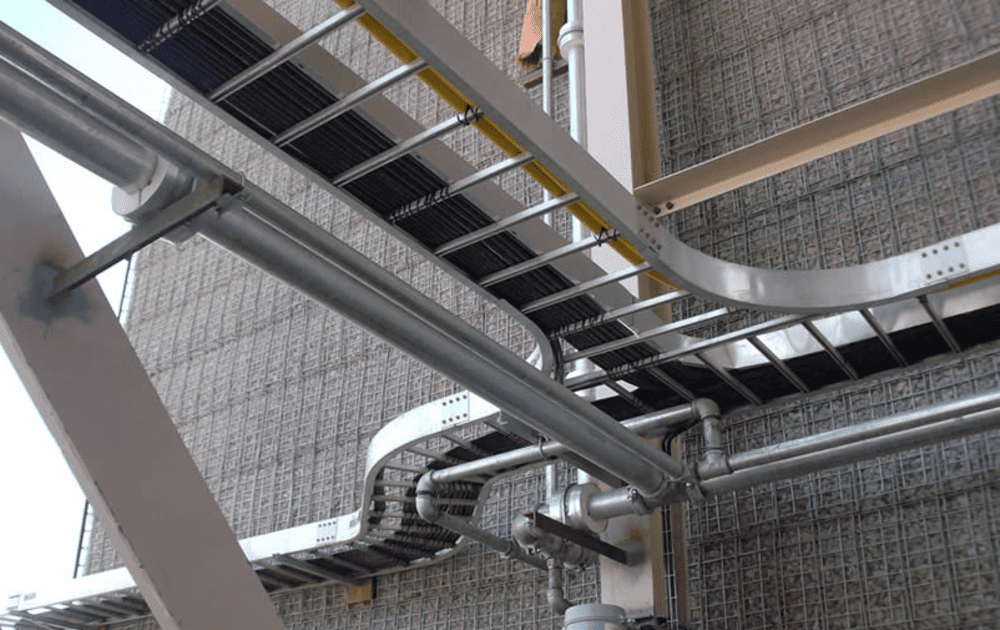
A proper cable tray system keeps electrical wires organized and supports safer, faster, and more efficient setups. Selecting the right one is vital for reliable operation.
Ladder and perforated wire trays are two of the most commonly used types. Though similar in appearance, they serve different purposes. A ladder cable tray offers better ventilation for heavy loads, while a perforated tray provides continuous support and a cleaner look.
This comparison explains the differences and how to select the right system for your project. It also includes tips for sourcing hardware and finding cable tray suppliers in UAE.
What Are Ladder Wire Trays
These are open-frame systems with two side rails connected by horizontal rungs. They are built from aluminum, galvanized, or stainless steel and handle heavy wires over long distances. The open design prevents heat buildup, protecting cable safety.
Frequently utilized in:
- Industrial facilities
- Electrical substations
- Energy sector
- Commercial-grade settings
Understanding Perforated Cable Trays
These trays have a solid bottom punctuated with holes or slots to promote airflow. They also allow cable fixing and access along the tray. Made from mild steel, aluminum, or pre-galvanized steel, they can be powder-coated or hot-dip galvanized for durability. They support light to moderate wire loads and suit flexible installation needs.
These trays are often used in:
- Commercial buildings
- Data centers
- Communication rooms
They offer a neat appearance, good airflow, and easy maintenance access.
Quick Comparison
Feature | Ladder | Perforated |
---|---|---|
Load Capacity | Handles heavy loads over wide spans, ideal for industrial settings. | Supports moderate loads in commercial environments. |
Airflow & Ventilation | Open design ensures excellent airflow, reducing heat buildup. | Provides good circulation but less than ladder trays. |
Ease of Installation | Lightweight with spaced rungs for faster installation. | Easy to install and flexible in tight spaces. |
Cable Support | Supports wires at intervals with strong rungs. | Provides continuous bottom support for delicate cables. |
Cost | Higher upfront investment for critical applications. | More affordable, balancing performance and appearance. |
Ideal Applications | Factories, oil refineries, power plants. | Offices, malls, hospitals, IT rooms. |
Maintenance Tips for Cable Tray Systems
Keeping your cable tray system in good shape ensures safe electrical operation and prevents costly downtime. Proper care also extends the life of your electrical infrastructure, especially in commercial and industrial settings where cable trays handle heavy wiring loads. Follow these easy-to-implement maintenance practices to keep everything running smoothly:
Inspect for Physical Damage and Deformation
Make it a routine to visually examine trays for sagging, bent metal, or structural wear. Look closely at the support arms, rungs, and side rails for cracks, breaks, or loose bolts. Damaged trays can compromise cable support and increase fire risk.
Keep the Cable Pathway Clean
Dust, dirt, and leftover debris from installations can accumulate inside trays. This buildup restricts airflow and may lead to overheating of power cables or data lines. A clean tray allows proper ventilation, enhances cable performance, and supports system cooling.
Check for Corrosion and Moisture Damage
If your trays are installed in humid areas, near HVAC systems, or outdoors, regularly look for rust patches or signs of oxidation. Galvanized steel and aluminum trays are especially prone to corrosion over time. Touch-up coatings or rust inhibitors can be applied to extend their lifespan.
Secure Loose Brackets & Fasteners
Over time, vibrations from nearby equipment or thermal expansion can loosen support hardware. Gently shake each tray and feel for movement. Tighten wall mounts, ceiling hangers, and clamps to keep the tray stable and maintain its load capacity.
Balance the Cable Load Evenly
Do not cluster too many wires in one section of the tray. Uneven cable distribution can lead to tray bowing or mechanical strain. Arrange cables in layers, keeping heavier wires at the bottom and maintaining space for airflow and future expansion.
Clear Entry and Exit Points
Ensure other wires or tools do not block cable entry and exit locations. Clear access simplifies maintenance, reduces the chance of cable damage during system upgrades, and makes it easier to identify issues when troubleshooting.
Pro Tip: Use a Maintenance Log
Keep a digital or physical log of every inspection. Keeping records helps spot recurring problems, avoid failures, and stay compliant during safety audits.
Final Thoughts
Selecting the right electrical tray is crucial for efficient cable management. Ladder trays offer superior load support and airflow for industrial setups. Perforated trays fit lighter commercial projects needing neat layouts and reliable support.
Evaluate load, ventilation, and durability needs before choosing.
Need help choosing the right tray?
BonnGulf is ready to assist you in selecting the best solution for your project.