- Home
- Common Mistakes to Avoid During Cable Tray Installation
Common Mistakes to Avoid During Cable Tray Installation
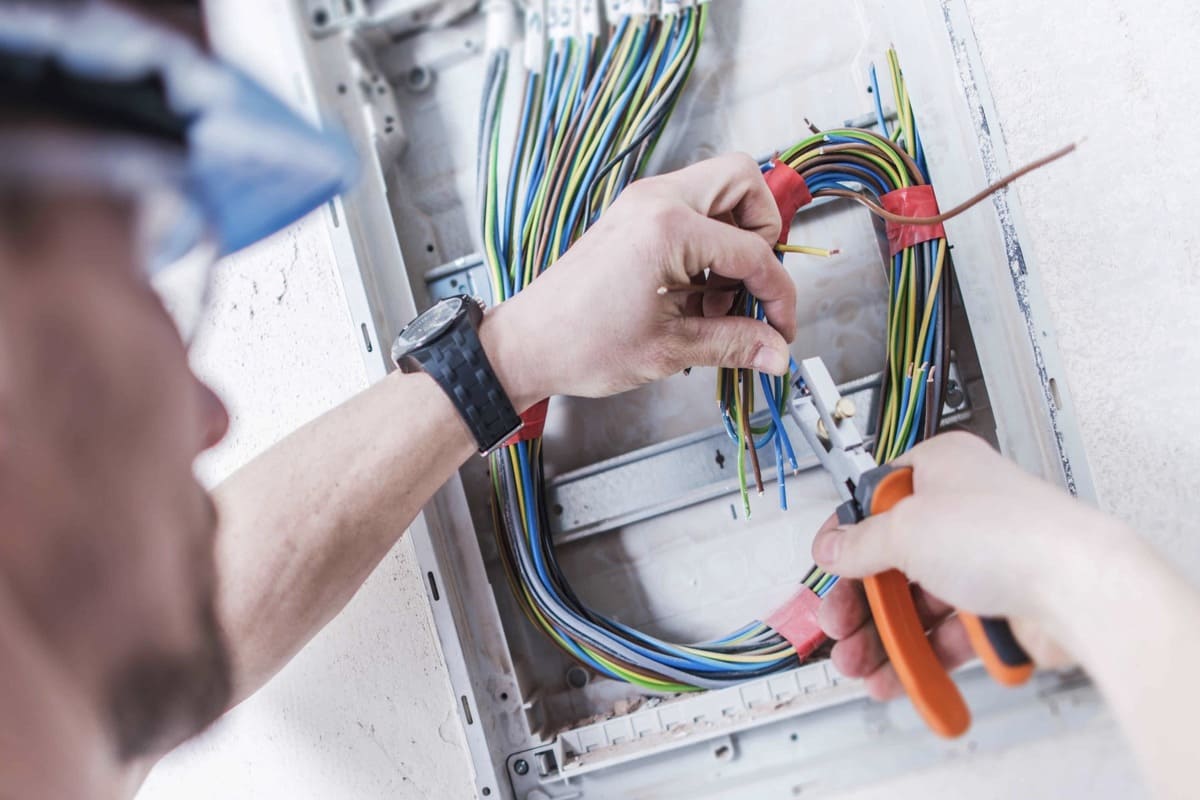
Every efficient facility relies on strong cable management. Cable trays help organize power and communication cables and keep operations running without issues. Durability means little when installation practices fall short.
Installation quality directly impacts system lifespan, efficiency, and regulatory compliance. Simple oversights like too much load or poor support spacing can be avoided with attention to detail. As one of the leading cable tray manufacturers in UAE, BonnGulf is committed to getting it right the first time. Our expertise helps businesses across the region build safer and smarter infrastructures.
Why Correct Installation Is Essential
Your cable tray system is a foundation for electrical safety and efficiency. Poor installation puts that foundation at risk, often resulting in downtime, hazards, and higher costs.
Safety Comes First
Incorrectly supported trays or exceeding load capacity can cause sagging or complete structural failure. It creates dangerous conditions like exposed wiring, cable insulation damage, and electrical shorts. Proper support spacing, secure fastening, and effective grounding are crucial steps that reduce shock risks and protect maintenance crews and nearby equipment. BonnGulf follows strict safety standards to ensure your system holds up under real-world conditions.
Designed for Maximum Efficiency
Too many cables in one tray or placing trays close to hot equipment leads to trapped heat. If airflow is blocked and thermal insulation is missing, cables can overheat. This, in turn, shortens life expectancy, raises energy losses, and risks failure. Careful routing, generous spacing, and proper ventilation improve safety and system cost-efficiency.
Smarter Maintenance, Fewer Headaches
Disorderly trays and missing labels can make a basic cable inspection a lengthy process. Keeping routing neat, labels readable, and trays accessible helps technicians work faster. Whether replacing a cable or resolving a fault, a structured design significantly reduces downtime and labor costs.
Built to Meet Every Code
Electrical systems must follow strict regulations, like those in the IEC (International Electrotechnical Commission). Improper tray spacing, lack of grounding, or overloading can quickly put you out of compliance. That means failed inspections, project delays, and even legal risk. BonnGulf ensures code compliance is built into every installation, helping you pass audits and operate safely without stress.
Top Mistakes To Be Aware Of
Avoiding these common cable tray installation mistakes can improve safety, reduce downtime, and extend the life of your system. Here’s what to watch for:
Poor Tray Selection and Planning
One of the most frequent missteps is selecting a tray type without considering installation needs. For example, using a tray that can’t handle environmental factors like humidity, chemicals, or heat can lead to early corrosion and failure. Similarly, ignoring airflow requirements may cause cables to overheat. Always match the tray material and design to the environment, cable type, and load expectations.
Overloading and Overcrowding
Loading a tray beyond its rated capacity leads to sagging, bending, and even collapse over time. It also makes it harder to organize or replace cables later. Overcrowded trays block airflow, raising the risk of overheating and signal interference. Always calculate total cable weight in advance, leave space for growth, and stick to fill limits.
Inadequate Structural Support
Trays that aren’t properly supported tend to sag or shift, especially under heavy loads. This stresses not only the tray but also the cables it holds. Following the manufacturer’s guidelines for support spacing is essential for maintaining integrity and reducing long-term stress on the system.
Electrical Safety Oversights
Neglecting grounding and bonding increases the risk of electrical faults and code violations. Trays must be grounded correctly and include bonding jumpers to maintain electrical continuity and safety. It is especially important in sensitive or high-voltage setups.
Routing and Future-Proofing Errors
Poorly planned tray routes, such as paths with tight turns or physical obstructions, can make installation difficult and maintenance frustrating. Misaligned trays also put pressure on cables, increasing wear. You may face costly rework if you don’t plan for future expansion. Always leave room for future cables and design clear, accessible routes from the start.
Best Practices for Flawless Installation
A successful cable tray installation is about understanding how each step affects safety, performance, and future scalability. Here’s a detailed checklist to guide every phase of your installation:
Plan the Layout Before Lifting a Tool
Before mounting trays or pulling cables, carefully map the cable route. Walk through the site, identify where equipment will be installed, note ceiling height changes, structural beams, HVAC ducts, or anything that could interfere with tray paths. This upfront planning avoids last-minute surprises and ensures your system follows the most efficient and practical route.
Select a Tray That Matches the Environment and Load
Not all trays are created equal. If your cables are heavy or span long distances, ladder trays provide strong support and durability. Wire mesh trays are lighter and easier to adjust for tight spaces or frequent reconfigurations. Use stainless steel or corrosion-resistant finishes in environments with moisture, chemicals, or high temperatures. Matching the tray type to the job conditions ensures longevity and performance.
Calculate the Load And Leave Room for Growth
It’s not enough to handle the current load. Your tray must support both today’s cables and tomorrow’s upgrades. Calculate the total cable weight and check it against the tray’s rated capacity. Then, add a margin for future expansion. Overloading leads to structural stress, sagging trays, and even cable damage. A forward-thinking approach now prevents costly rebuilds later.
Use the Right Support Spacing to Prevent Sagging
Cable trays need support at regular intervals to hold weight evenly and avoid deformation. Most trays require support brackets every 1.5 to 3 meters, depending on the tray size and expected load. Too much distance between supports allows trays to bend, putting stress on the tray and the cables. Proper spacing keeps everything level and secure.
Ensure Reliable Grounding and Bonding
Electrical safety isn’t optional. Connect bonding jumpers at every tray joint to ensure continuous grounding throughout the system. It protects people and equipment from electrical faults and ensures compliance with safety standards like IEC 61537. Your tray can become a hidden hazard during a fault or surge without grounding.
Avoid Overfilling (Protect Airflow and Cable Life)
When trays are overcrowded, heat builds up, airflow is restricted, and cable insulation can degrade. It also makes troubleshooting or replacing cables more difficult. Respect the cable fill limits defined by standards and manufacturers. Leave space between bundles to allow air circulation and technicians to work comfortably.
Install Trays Where They Can Be Reached Easily
A beautiful installation means nothing if maintenance is impossible. Don’t run trays above false ceilings, behind fixed walls, or in corners requiring ladders or disassembly. Choose tray routes that are visible, open, and safe to access. It will save time and effort every time you inspect, clean, or upgrade the system.
Document Everything for Long-Term Success
Once the installation is complete, take time to record every detail. Create layout diagrams, list cable types, label tray sections, and note load calculations. This documentation isn’t just for now; it’s a vital resource when expanding, upgrading, or troubleshooting the system in the future. Good records turn one-time work into lasting value.
Conclusion
Proper tray installation delivers safer, more reliable systems with fewer maintenance headaches. Using the right materials, careful planning, and proven best practices makes all the difference.
At BonnGulf, we don’t just manufacture cable trays. We help you build better infrastructure. Our solutions are engineered for real-world demands and full code compliance.
Are you looking for a trusted cable tray supplier?
Contact BonnGulf today for high-performance products and expert support.